Our source power
Lean management to build a century old enterprise
The spirit of ingenuity inherits the corporate culture
Good products are inseparable from
High quality raw materials
Exquisite workmanship
Quality control
Meiki minhy, committed to being around you
The most trusted hardware enterprise
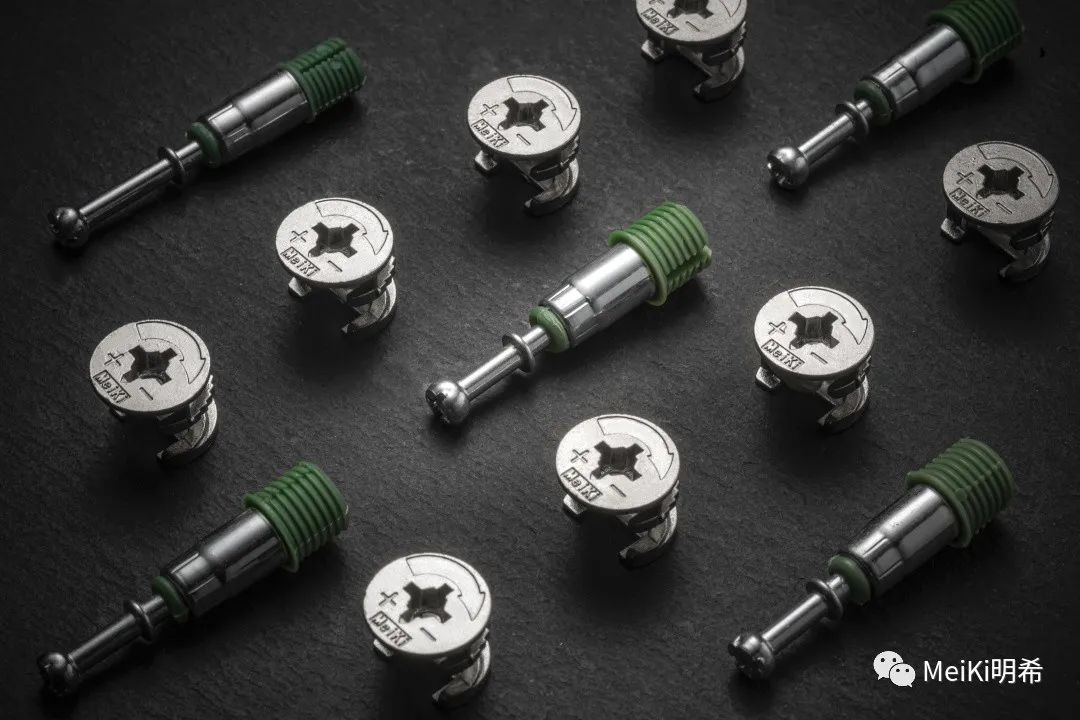
The following pictures and words are fully displayed for you Wonderful process of zinc alloy products from scratch
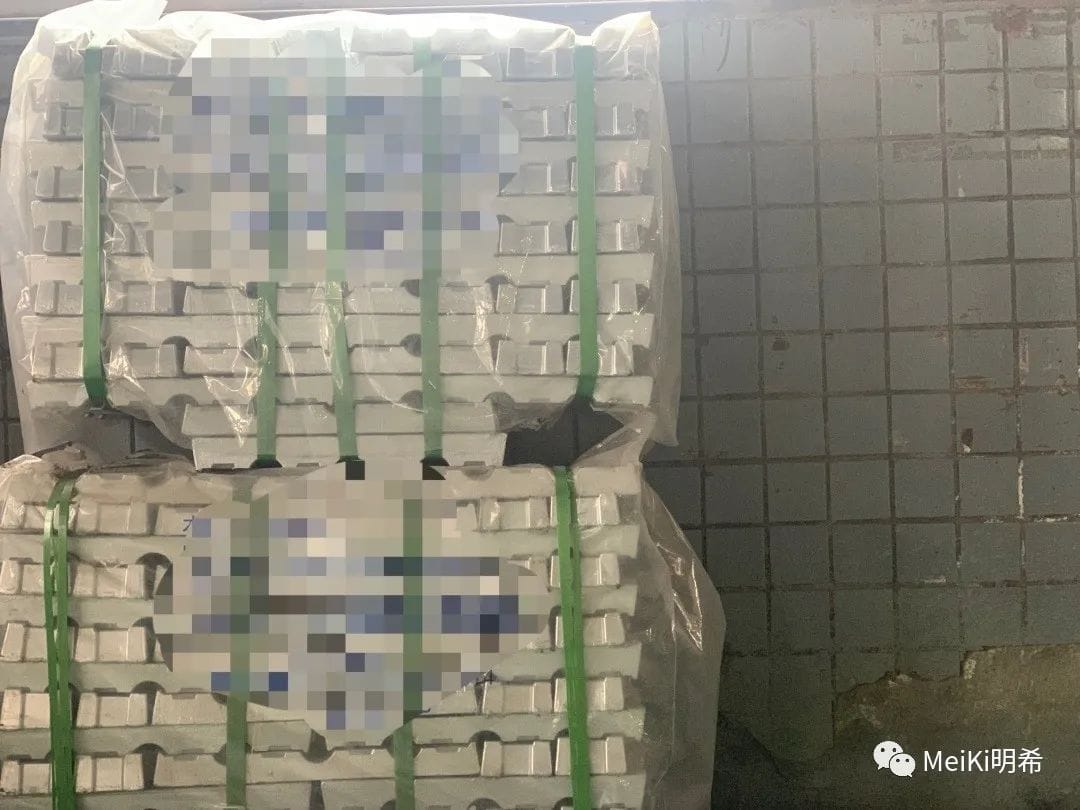
1. Raw material link
Grasp the source and strictly select high-quality products
It is an alloy composed of zinc and other elements.
Low melting point, good fluidity, easy fusion welding and plastic processing
Corrosion resistance in the atmosphere.
Features: good casting performance, with complex die-casting shape,
Thin wall precision parts with smooth casting surface.
Zinc alloy selection considerations:
1). For the purpose of the product itself, the service performance requirements to be met: mechanical properties, tensile strength; Working environment status: temperature, humidity, medium contacted by workpiece and air tightness requirements; Precision requirements: the precision and dimensional stability that can be achieved
2). Good process performance
3). Good economy: cost of raw materials and requirements for production equipment
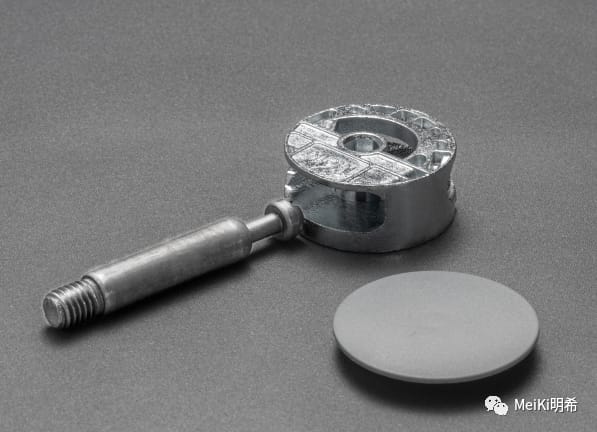
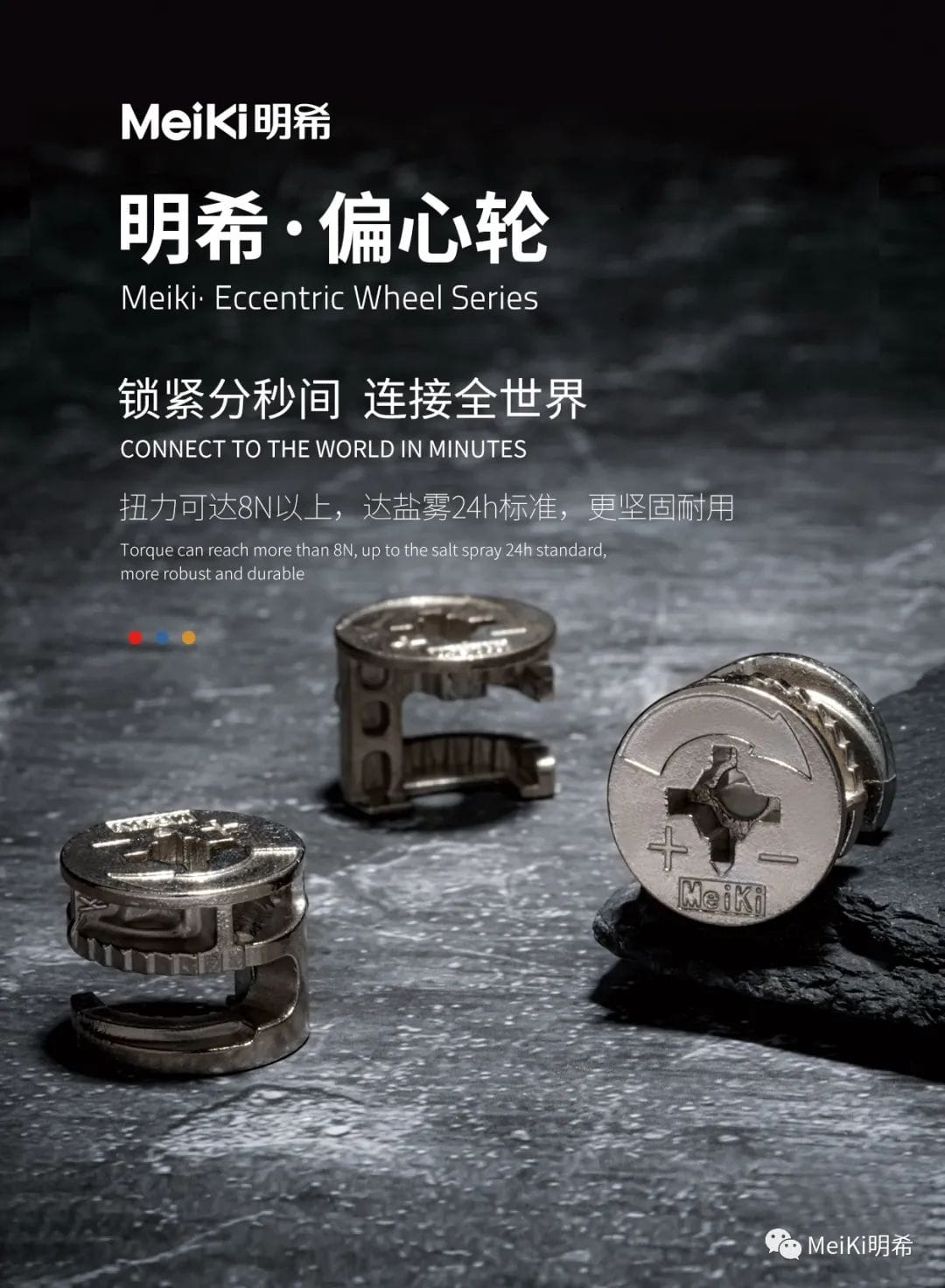
2. Die casting workshop
High configuration | high quality
Our company mainly uses zinc alloy to cast eccentric wheels and other die-casting products
Product principle:
As one of the components of three in one connector, eccentric wheel is the most important connecting accessory. Using the radian of the bottom torsion bending angle deviating from the center of the circle, when the cross screw groove on the surface is rotated, the connecting rod clamped in the radian will be pulled to the center of the eccentric along the radian, so as to make the connecting rod tighten the distance between eccentricity and anti-skid embedded rubber particles, so as to fasten the connection between plates
3. Production process
Automation | high quality
1). Raw materials inject molten metal hydraulically into the mold for cooling and forming through the pressure of the die casting machine. After opening the mold, solid metal castings can be obtained (in this process, the machine operator can observe the state of the machine at any time to ensure normal operation and do not affect the product forming) (the quality inspector can inspect the formed products at any time and stop the machine for treatment at any time in case of quality problems) (the mold workshop can cooperate with the mold repair and improvement in time)
2). The finished products go through electroplating processes such as nickel plating and blue white zinc to increase the corrosion resistance, hardness, wear prevention, smoothness, heat resistance and beautiful surface
3). Finally, perform burr treatment again
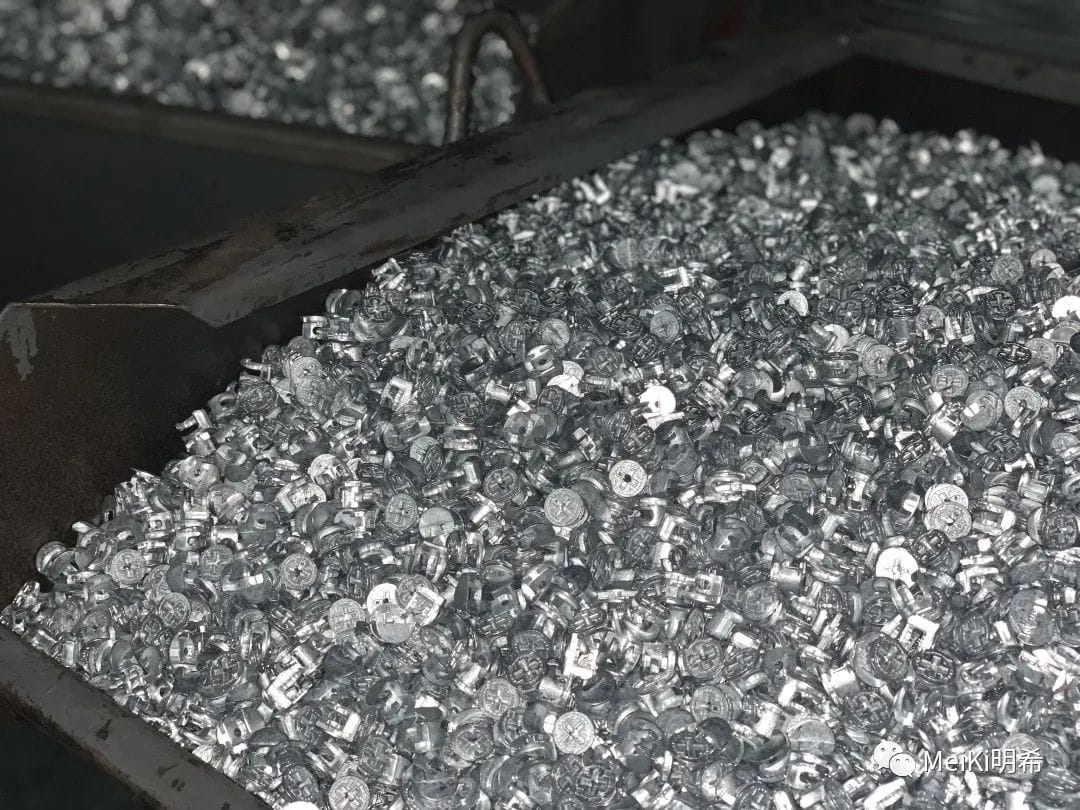
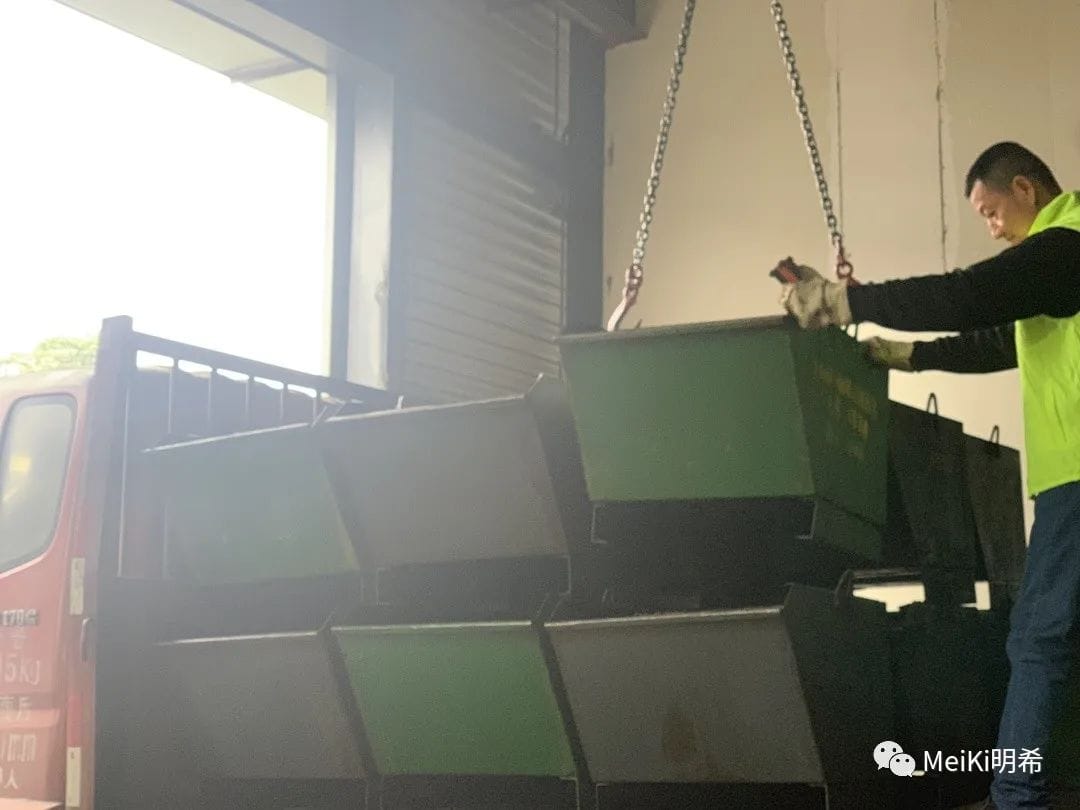
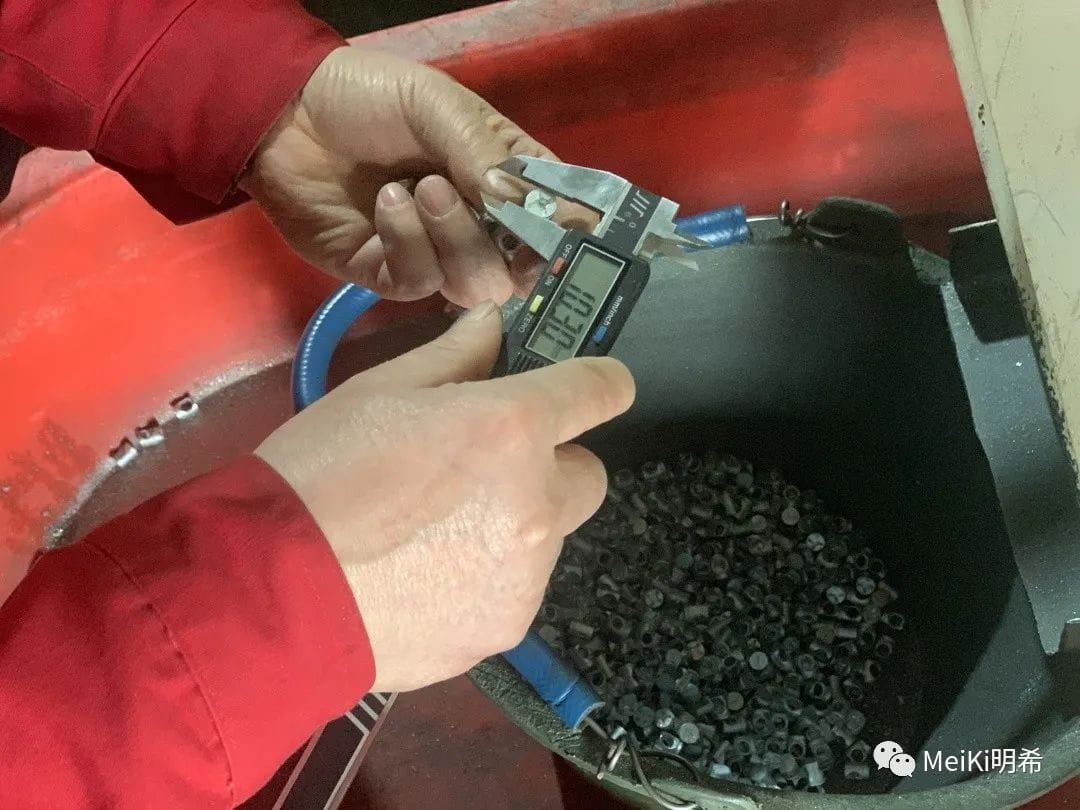
4. Finished product packaging
Automation | high efficiency
Packaging is the final ring for the output of finished products. If there is a quality problem in the packaging, even if the product is produced No matter how good the quality of the product is, customers will reject the whole product because of the bad impression of the packaging Yes. So the more the last minute, the more attention.
Bagged products are not short of weight
The packing bag is waterproof and fall proof
Cartons are thickened and not easy to break
Can experience long-distance transportation and bad weather
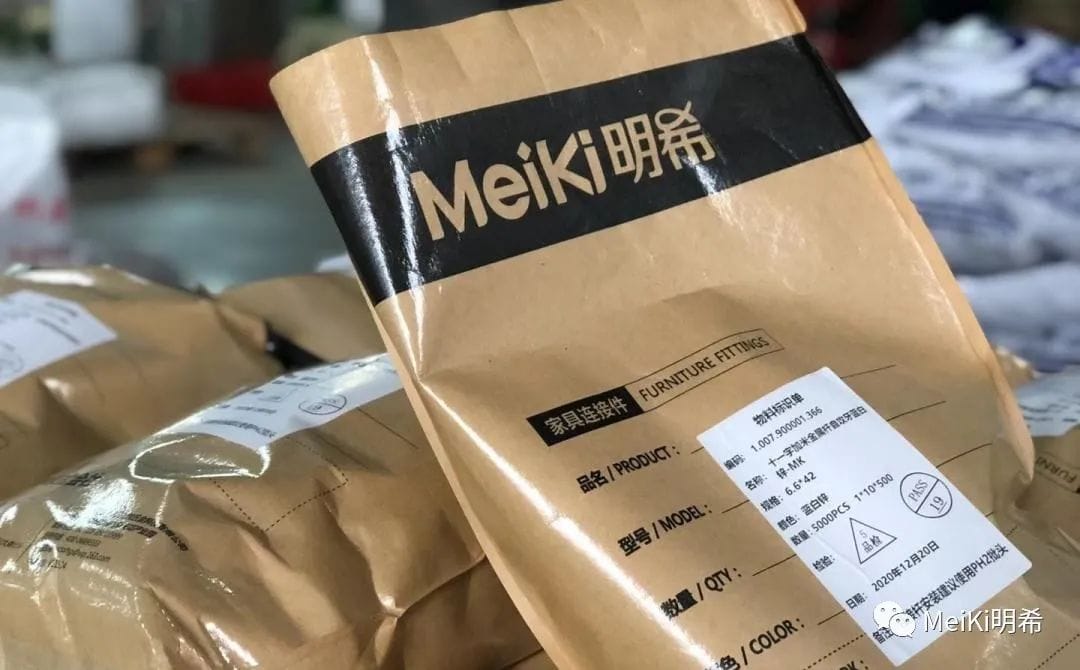
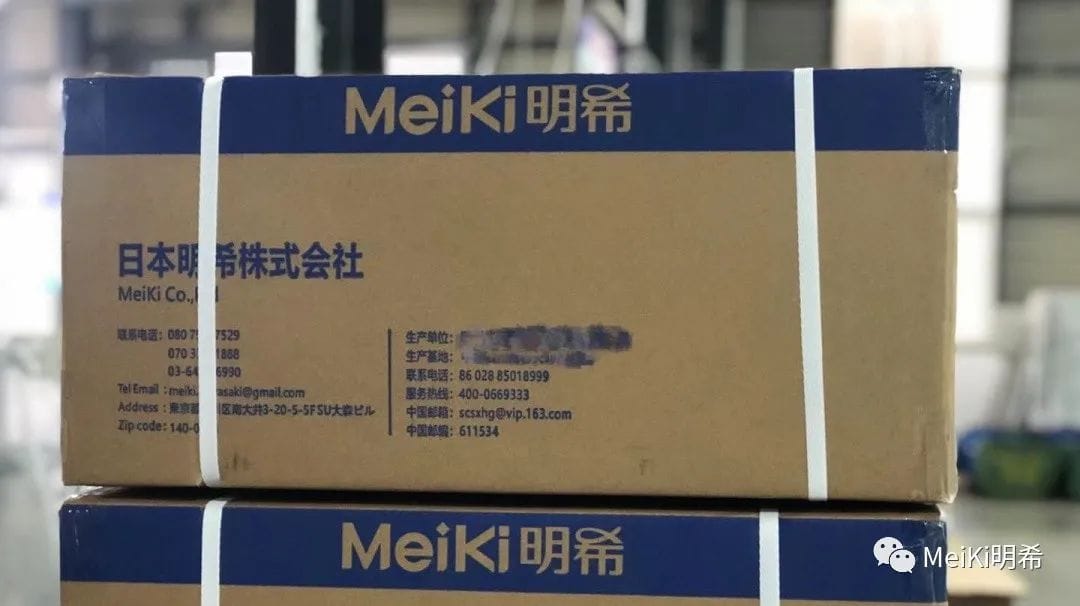
5. Storage and transportation
Timely shipment | arrive on time
We have a mature logistics distribution system to meet customers' pursuit of timeliness
Southwest market: finished products are warehoused on the same day, loaded on the same day and delivered the next day
Markets outside the province: logistics delivery twice or three times a week
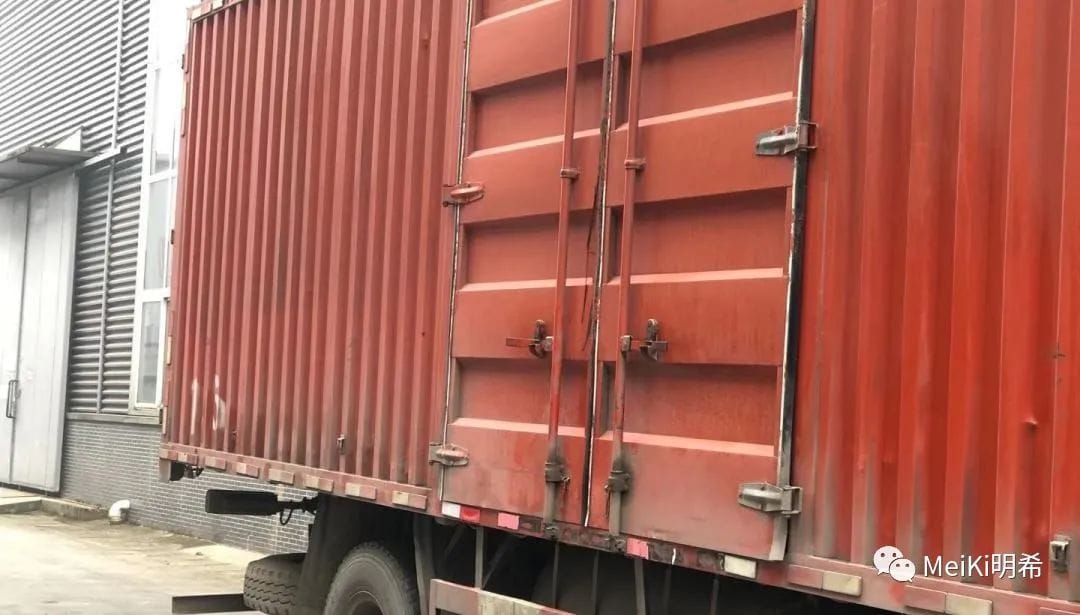
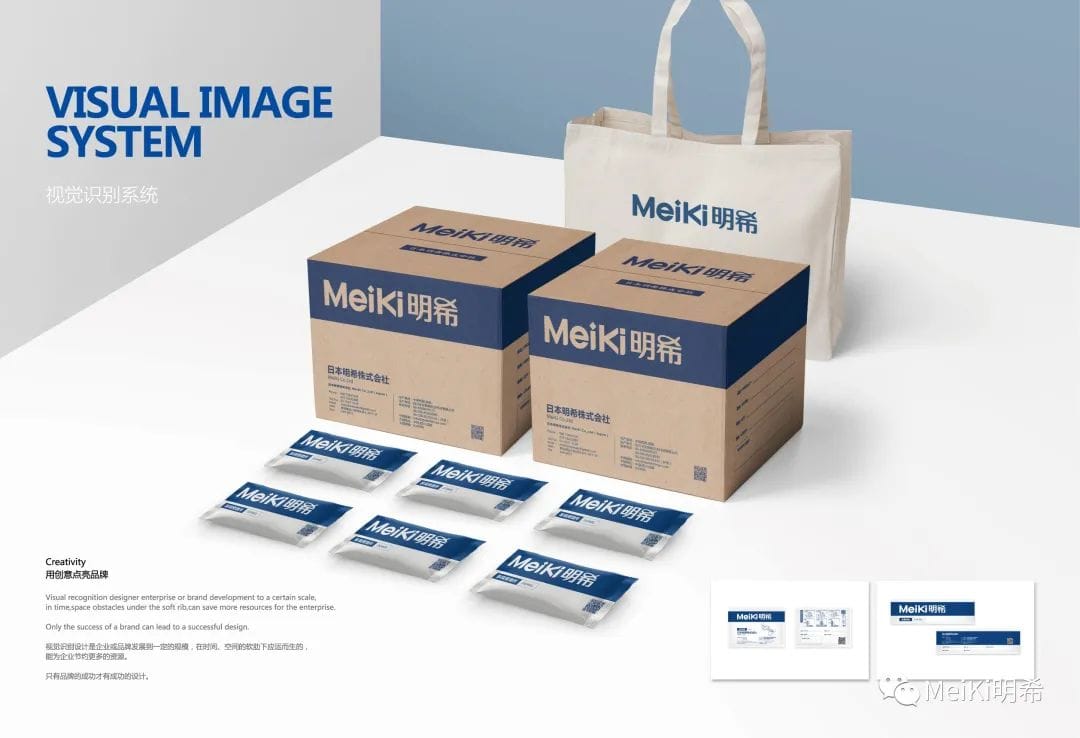
Survival by quality, Seeking development by benefits
Post time: Mar-21-2022